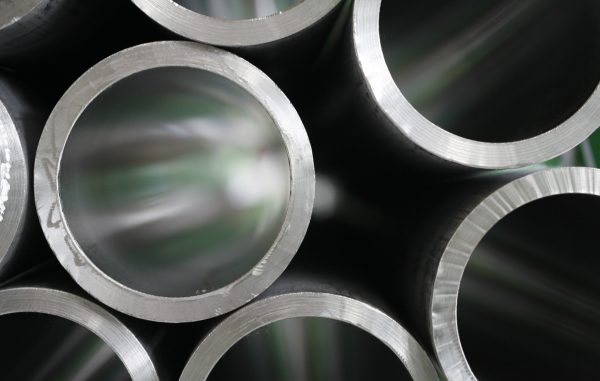
Division of pipes based on pipe ends execution
Different applications of steel pipes necessitate different machining of their ends. Therefore, the following types are distinguished:
– pipes with threaded ends: pipe thread (Whitworth or Briggs), thread for drill stems (Briggs),
– pipes with smooth ends – represent the largest group due to welded connections,
– flare ended tubes – (used less frequently, mostly in carrier pipes),
– pipes with rims for loose flange (used less frequently, due to common welding practices).
The most popular dimensions of steel pipes
Basic dimensions of steel pipes include outer diameter and wall thickness. These are normalized parameters due to the intended use and production technology. Internal diameter of a pipe is a function of the basic parameters.
Dimensions of individual pipes are created according to a specified system, wherein outer diameters are related to pies wall thickness ranges. The whole must be adapted to a specified intended use. Profitability of production and application of pipes is also considered.
In the first place, carrier pipes dimensions have been systematized. The remaining types of pipes were dependent upon the carrier ones, because they were made using the same machines.
In Great Britain, the range of carrier pipes was classified after introducing Whitworth thread with flank angle 55°. At the moment, pipes specified based on English principles are commonly used in Europe.
In the United States, standards introduced by the American Petroleum Institute are used. Carrier pipes and drill stems are classified based on Brigss thread of flank angle 60°. Drill stems according to API have been adopted globally.
In Poland, the range of diameters for pipes designed for threading is accepted based on Whitworth thread. Pipe wall thicknesses are adopted for thread tapping. Due to forces necessary to tap and connect the pipes, pipes of diameter above 4” are not connected via threading (according to DN100) in Poland. Diameters of pipes and their thickness used in threaded connections are presented in Table No. 2.
Division of pipes based on their cross-section
Based on the cross-section shape, the pipes can be divided to:
– round,
– rectangular,
– square;
– polygonal,
– elliptic,
– droplet,
– other.
Based on the wall thickness, the following pipes types are distinguished:
– fixed wall thickness,
– varying wall thickness,
– pipes with extruded external ribs,
– pipes with extruded internal ribs,
– rolled, extruded ribs (straight, needle-like, spiral),
– ribs wound and welded from tapes.
Division of pipes based on the applied protective surface coating
Most of the pipes are produced without a protective coating. This group includes black and white pipes.
Black pipes represent the greatest produced range. Their surface is covered with a thin layer of oxides, scale. A thin layer of corrosion may also be present. They are protected against corrosion after completion of a system or they are use without paint coatings, such as pipes in boilers, due to temperatures.
White pipes these are mostly structural pipes satisfying high surface quality requirements. They are cold treated, hot treatment is possible within protective atmosphere, and they require post-treatment cleaning. White pipes may be covered by protective greases.
Depending on the type of a protective coating, two types of pipes are distinguished:
– pipes with metallic protective coatings – these are mostly galvanized pipes used in hot and cold water systems. Such pipes are exposed to corrosive properties of water and frequently are covered with double galvanized coating. Coatings including other metals are also used – especially for industrial pipes.
– pipes with non-metallic coatings (enamelled, lacquered or coated with asphalt). Enamelled pipes are used mostly in the chemical sector. Asphalt coated pipes have large diameters and are applied in the construction of long-range pipelines of water, gas or petroleum.
Moreover, there are pipes with protective lining: ceramic, of plastic compounds (rubber, PVC), as well as plated pipes, coated with high strength metal coating. Protective lining of ceramics or rubber must be applied on pipes subjected to severe abrasion, present e.g. during transport of water and quartz mixes. Plated pipes and pipes with lining of plastics are mostly used in the chemical sector. This reduces the use of stainless steel and minimizes the overall system costs and extension of its life.
Division of pipes based on production technology
Considering the production technology, two basic steel pipe groups can be distinguished: seamless pipes and seam pipes. Each of these groups can be characterized by a production method (hot production,
cold production).
Seamless pipes are cold or hot rolled or drawn pipes. Seamless pipes can be produced up to 508 mm diameter. Seamless pipes within the range of diameter between 500 and 800 mm are seldom produced. Pipes of diameter above 800 mm are manufactured with seam only. This is because there is no significant demand for seamless pipes of large diameters on the market. The production technology of seam pipes has improved.
Hot rolled or drawn pipes have minimum outer diameter around 20 mm. They have less dimensional precision and worse outer surface.
Cold rolled or drawn pipes have less range of outer diameters. Diameters are within a range between 3 mm and ca. 200 mm. They characterize with less wall thickness that cannot be obtained using hot production methods. Much greater dimensional accuracy and surface quality is provided. Moreover, they may attain better mechanical properties due to cold work.
Seam pipes can be divided based on the production technology. There are pressure welded pipes (electrically: resistance or induction) and welded pipes (e.g. electrical arc in argon or hydrogen shield).
Pipes with straight seam have small diameters and pipes with spiral seam are made in large diameters. Seam pipes can be subjected to forming processes or to removal of flash, like pressure welded pipes.
The origins of steel pipes production
Until 19th century, pipes were mostly made using soft and plastic metals, i.e. lead. The first important incentive related to development of steel pipes production technology was the first in the world installation for lighting gas. It was made in London, around 1815 (after Napoleonic Wars). The construction has been made of rifle barrels connected using a thread. Conical shape of a barrel allowed for providing outer thread on the thinner end and internal thread on the thicker end (at the lock). Pipeline clearance was ca. half inch. The necessity to develop such a pipeline as well as construction of new ones (in other London districts and other cities) raised the demand for steel pipes.
Production of butt welded pipes of outer diameters up to 76 mm has been patented in Great Britain in 1825. However, in 1842 by patenting, in the same country, pressure welded pipes with overlap, production of pipes of outer diameters up to 305 mm has been started.
Thread standardization has also originated in Great Britain. In 1841, a pipe thread standard has been developed for pressure welded pipes, which in many countries is in force to this day, only with minor changes. Thread was named by the creator of the standardization and is commonly known as Whitworth standard. Pipe diameters related to this are applied in Europe to this day (threaded installation pipes).
In USA, threads and pipes standardization took place somewhat later – in 1862. Briggs thread was introduced then, and it is still valid.
Division of steel pipes based on application
Depending on applicable essential parameters, the following pipes classification is adopted, based on:
– application,
– production method,
– cross-section shape,
– type of protection film and surface quality,
– pipes ends treatment,
– steel grades,
– acceptance test scope,
– production precision.