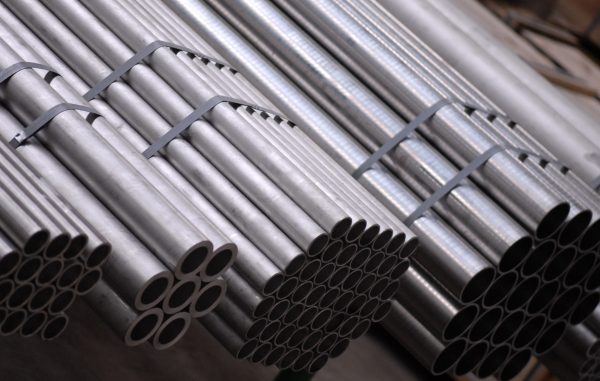
Alloying elements in steel
Chemical composition decides about steel properties. Alloys of iron and carbon as well as other elements, i.e. alloying additives, are used to obtain it. Their quantity should exceed the minimum concentration, at which there are no changes in the properties or structure of steel. The most common alloying additives are as follows: nickel, titanium, vanadium, chromium, silicon, molybdenum, tungsten, cobalt, aluminium, copper, niobium and manganese.
Alloying elements are introduced not only to provide specified properties but also to increase hardenability, facilitate heat treatment, improve resistance to corrosion and wearing as well as enhance physical, physicochemical, technological and mechanical properties. Each of the additives changes the steel properties differently. Not all of them may have positive impact that is why there are useful and harmful additives.
Molybdenum increases resistance of steel to corrosion. In case of austenitic acid-proof steels, its content is about 2.5%, but could reach even 7%. This element is responsible for improvement of strength and hardenability, reduction of fragility and increase of creep strength.
Copper can be characterized by similar physical properties as iron, but it is much less susceptible to corrosion. Addition of this element is more and more appreciated, especially when it comes to melting new steel.
Nickel not only facilitates hardening process and improves its depth, but it also reduces the temperature of austenitic transformation and after melting down in ferrite, strengthens steel and improves its resistance to impact. The element is an important component of acid-proof steel, because it provides good weldability and plastic processing. Nickel in amount 0,5% – 4% is added during quenching and tempering, however above 8% – 10% is added to acid-proof steel.
Chromium like nickel it affects steel hardenability and increases its strength and contributes to grain size fragmentation. As an additive, it is frequently used in structural, heat-resistant, stainless and tool steels. In case of stainless steel, chromium is the element that decides about resistance to corrosion. Content of this additive varies between 12% and 30% – depending on the steel grade.
Silicon is perceived as an undesirable additive, it affects fragility, hardness, elasticity and strength of steel. Admixture of silicon is the most common in spring steel, it reduces resistance to impact and improves resistance to high temperatures. The element is added to the steel grades that operate under high temperatures and are in contact with concentrated nitric or sulphuric acid.
Manganese beneficially affects the steel strength to impact and abrasion, at the same time changing its ductility. This is the element that makes steel stronger.
Among harmful additives, one must mention first and foremost sulphur that impedes steel forging and phosphorus that reduces strength and resistance to impact, increases its hardness causing fragility at low temperatures.
Based on the share of alloying elements, steels can be divided to:
– low-alloy – of concentration of a single element less than 2%
– medium-alloy – of concentration of a single element less than 8%
– high-alloy – of concentration of a single element more than 8%
Based on application, there are:
– tool steels
– structural steels
– special-purpose steels
Special purpose steels can be characterized by high resistance to corrosion and can be classified according to the structure (ferritic, martensitic, martensitic precipitation hardening, austenitic as well as austenitic and ferritic) as well as based on chemical composition (high chromium, chromium and nickel as well as chromium-nickel-manganese).