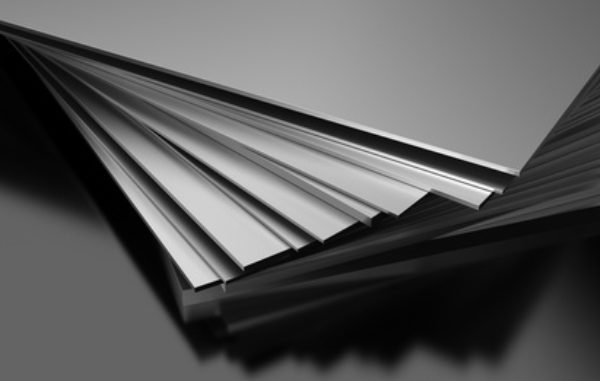
The main difference between heat-resistant and stainless steels is their indented use. The basic operational feature of stainless steels is the resistance to corrosion. Application of this steel grade may take place either under room conditions, significantly negative temperatures or even up to temperature ca. 500°C. Under such conditions, grades highly resistant to material corrosion must be used. Mechanical properties are much less important under such circumstances. In the past, the steel was divided to stainless steel and acid-proof steel. Now, stainless steel means any steels that show resistance to corrosion and at the same time are not heat-resistant (creep resistant) steels.
In case of heat-resistant steels, the basic feature of the material is its good resistance to corrosion at temperature exceeding 500°C. The heat-resistant steels must show very good mechanical properties at temperature exceeding 500°C. This is related to resistance of the material to slow deformation of stresses lower than yield strength of the material, i.e. creep strength.
The group of steels resistant to corrosion includes stainless, acid-proof and heat-resistant steels. Designation of stainless steel grades covers the range between 1.40 and 1.45. Acid-proof and heat-resistant steels are identified with the numbers from 1.47 to 1.48. To sum up, stainless steels can be used at temperatures up to ca. 500°C. However, above 500°C, heat-resistant steels are applied. Under such conditions, materials are endangered to oxidation and corrosion.
One must remember that heat-resistant steels 1.4749 (X18CrN28) and 1.4724 (X10CrAlSi13) can be characterized by various weldability. In general, weldability of austenitic grades is higher than ferritic heat-resistant steels. Welding process of ferritic heat-resistant steels requires pre-heating (before welding) up to temperature ca. 100 to 300 °C. Moreover, after welding process, treatment is necessary that consists in annealing at temperature ca. 750-800 °C. The aforementioned requirements apply to such grades as: 1.4742 (X10CrAlSi18), 1.4762 and 1.4724 (X10CrAlSi13). Steel grade 1.4749 (AlSi446) has much better weldability. It does not require heat treatment directly after welding. In case of 1.4749 (AISI 446), it is necessary only to pre-heat to temperature ca. 200 to 400 °C.
Under certain conditions, stainless steels can be combined with carbon steels.
It is possible to combine stainless steel with regular one. In such a case, it is recommended to use a binder 309L (acc. to EN 1600 23 12 L R, acc. to AWS E309L). Such binder includes ca. 23%Cr, 13%Ni. It is designed to combine Cr-Ni stainless steel with low-alloy steel. During a welding process of stainless steel without molybdenum (1.4301, OH18N9) with low-alloy steels (carbon), the following wires are used: 309L-Si, 309L, 309L-HF. These are high-alloy wires ensuing welds resistant to cracking. Wire 309L is the most often selected to fuse stainless steel 304 with carbon steel.
Stainless steels can also be applied in building structures, among other things to reinforce walls with concrete. Because concrete is a porous material, it can be used for covering structures of steel resistant to corrosion. In this case, it is important to properly select steel grade for such application. There are specialist corrosion resistant steel grades that are recommended for concrete reinforcement. The most common grades are: EN 1.4301, 1.4429, 1.4462, 1.4436, 1.4501. Austenitic structure steels: 1.4429, 1.4301, 1.4436. Steels 1.4462, 1.4501 can be characterized by ferritic and austenitic structure (duplex). Reinforcement bars are made of the following stainless steel grades: EN 1.4436, 1.4429, 1.4301, 1.4462.