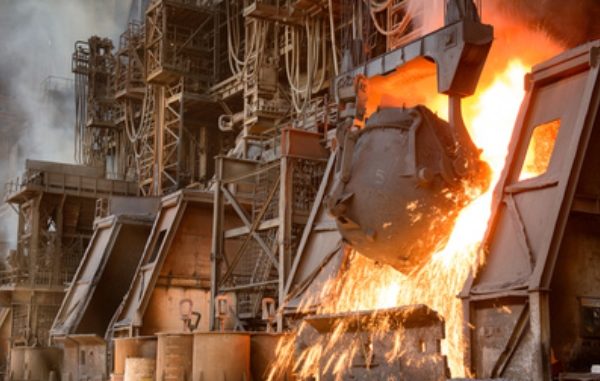
Machines used in the modern heavy industry are very resistant to high temperatures. Such parameters are provided by heat resistant steel used to produce many types of seamless pipes, sheets, railway and tram rails, hollow bars, sections, angles and other elements used for production of devices operating at high temperatures, for example boilers or industrial furnaces in mining, metallurgy, transport, civil engineering, automotive, foundry industry.
Heat resistance of steel is ensured by its chemical composition that can be characterized by high content of chromium and alloying additives, such as: molybdenum, tungsten, silicon and aluminium. Therefore, steel is reinforced with creep resistance properties, thus it is much more resistant to corrosive gases at temperature above 550°C. Due to technological reasons, steel is also enriched with small amounts of nickel (maximum 4%), which may decide about its structure. Steel is most often of ferritic-austenitic or ferritic structure that can be characterized by high susceptibility to fragility related to release of carbides at high temperatures (350-550°C).
Not only heat resistant or stainless steels are among the group of corrosion resistant steels but also acid-proof steels. Each of the grades has its own identification – heat resistant and creep resistant steels are identified with the number range from 1.47 – 1.48. When it comes to heat resistant steels, in case of ferritic grades, the whole process requires previous heating to temperature 100-300°C. Moreover, after welding operations, a machining is necessary which consists in annealing at temperature ca. 750-800°C. This applies to such grades as: 1.4742 (X10CrAlSi18), 1.4762 and 1.4724 (X10CrAlSi13). However, there are materials of much better welding properties, therefore, after the welding process, heat treatment is not necessary. Steel 1.4749 (AlSi446) has such features.
In order to evaluate the degree of heat resistance of a given material, specialist tests are performed – steel sample is heated for 24 hours to a specified temperature and then cooled to 20°C. Before the protective layer of scale is removed from the surface, the heating and cooling operation must be repeated five times. Then, the material is weighed in order to determine weight loss. This is the parameter that decides whether the tested steel has heat resistant properties. Heat resistance of steel can be improved by adding rare earth elements (lanthanum, cerium, praseodymium, neodymium), therefore oxides present in the protective layer will be more resistant to flaking, which is the direct reason for the material loss during operation.
In most cases, heat resistant steel also has stainless properties. The basic difference between them is their intended use. Stainless materials can be used both at negative temperatures, very high temperatures (about 500°C) and under room conditions. These features make them highly resistant to corrosion. Therefore, they can be applied in building structures, e.g. for reinforcement of walls with a concrete. When it comes to heat resistant steels, they are not only resistant to temperatures above 500°C, but also can be characterized by creep strength, i.e. slow change of material shape, resulting from stresses, lower than yield strength of a material.