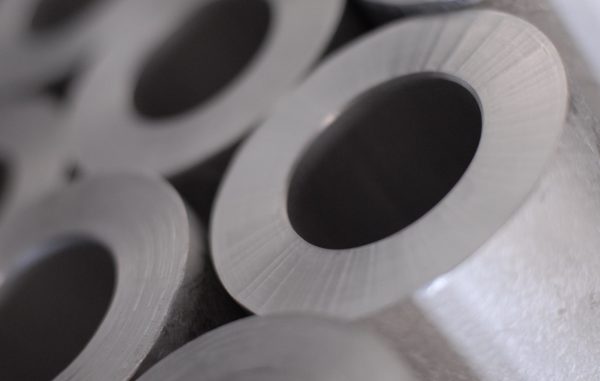
Grade specified as EN 1.4571 (according to European Standard) is stainless steel type 316Ti. This can be called the basic steel grade type 316 (1.4401) with a stabilizing additive. The additive is titanium. Titanium plays significant role in this steel. It is of special importance at the stage of heating the product to maximum temperature of 815°C. After application of titanium additive, the risk of intergranular corrosion drops. Titanium together with carbon creates proper carbides that allow for forming chromium carbides. Therefore, concentration of chromium remains at fixed level – thus the intergranular corrosion phenomenon does not occur.
What is the intergranular corrosion?
It takes place when a solution attacks boundaries of grains without affecting their interior. In other words, it is a selective dissolution of grain boundaries or adjoining areas as a result of a corrosive process. The factor causing this process is the difference of potential between the Cr (chromium) depleted grain boundary, in case of chromium carbides – anode, and an inclusion, intermetallic phase or contamination on a grain boundary. It depends on chemical composition and heat treatment. This corrosion starts at the surface and penetrates metal. Strength and ductility drop rapidly. Sample of metal affected by such a corrosion does not make metallic sound, and during bending – it breaks. In extreme case, it can disintegrate to powder. This type of corrosion is very dangerous. Accurate determination of this type of corrosion extent is very difficult. Evaluation of this corrosion is made using microscopic methods and through the increase of electrical resistance.
There is also another method of fighting intergranular corrosion. It includes radical change of carbon concentration in steel. This reduction drops down even to 0.03%. Using this method, another grade of steel was developed – specified as 316L (1.4404). Comparing to the basic grade 316 (1.4401), in this case carbon concentration was significantly reduced. Using such operations, steels 316T and 316L can be characterized by better resistance to intergranular corrosion.
Titanium contained in this steel grade 316Ti (EN 1.4571) increases mechanical properties at higher temperatures, above 590 °C. Therefore, within high temperature environments, application of steel grade 1.4404 is not always justified. Analogically, at room temperature applications, grade 1.4571 shows less susceptibility to forming than steel 1.4404. Moreover, grade 316Ti is more difficult to polish and has less machinability comparing to 316L. This is related to the presence of titanium carbonitrides in 1.4571. Weldability of both steel grades (316Ti and 316L) is similar. Differences within this field are not too perceivable.
Stainless steels 1.4404 and 1.4571 were tested at very low temperatures. Results show that both grades of steel can be used in cryogenics, because high impact strength is required in this area. At temperatures below 200 °C it is recommended to use low-carbon steel grades such as, among other things 1.4301 and 1.4404.
As opposed to classic austenitic steels, duplex and super duplex steels show much better tensile strength. Typically, it is about twice as high as the yield strength, however in case of austenitic steels, this ratio is only ca. 0.35. This comparison proves the benefits of duplex steel, because yield strength is the basic design measure for designers. In case of operation at higher temperatures, one must consider the drop of yield strength as a result of weakening of the strengthening impact of nitrogen. This is because the atoms of nitrogen dispersed in austenite become more mobile, thus they can block the dislocation movement to less extent.