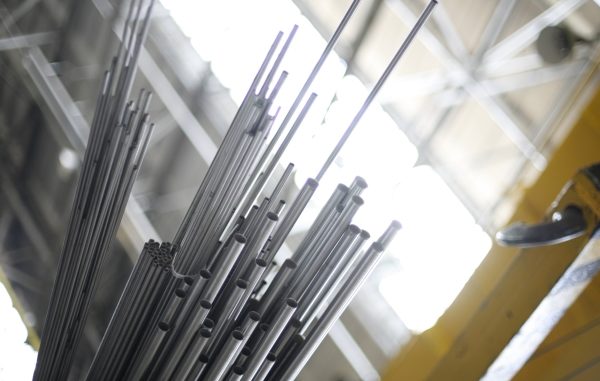
There are a few methods of chemical treatment of material surface. They are to provide clear, metallic surface.
- Etching
Etching process is used to remove oxides, first and foremost the coloured tarnish occurring as a result for material welding and other stains or corrosive tarnishes. The result of etching is clear, metallic surface that allows for an initiation of natural, self-acting passivation of stainless steel on the metal surface. The most common etching agents include nitric acid (HNO3) and hydrofluoric acid (HF). Time necessary for correct etching depends on solution temperature and its concentration.
- Passivation
Natural (self-acting) passivation of stainless steel takes place in the presence of oxygen included in water or air. Under natural conditions, the process is long-term and takes even a few days until the passive layer reaches sufficient thickness. Chemical passivation is used to accelerate the formation of passive layer and guarantees its quick growth until obtaining optimum strength. Passivation is performed in a solution of dissolved nitric acid and the treatment time ranges from a dozen minutes to one hour.
- Cleaning with acid or decontamination
The process involves removal of iron particles that undergo corrosion when located on a stainless steel surface. Such situation takes place when stainless steel elements are exposed to contamination, e.g. iron (dust after grinding, filings, corroded iron elements, etc.).
- Electropolishing
Electropolishing is applied after cleaning metallic surface, to reduce roughness and obtain many other required results. The process uses the electrolysis phenomenon that is why it requires a flow of current and application of an electrolyte, in most cases it is a solution of sulphuric and orthophosphoric acid. Electropolishing takes from a few to a dozen minutes.